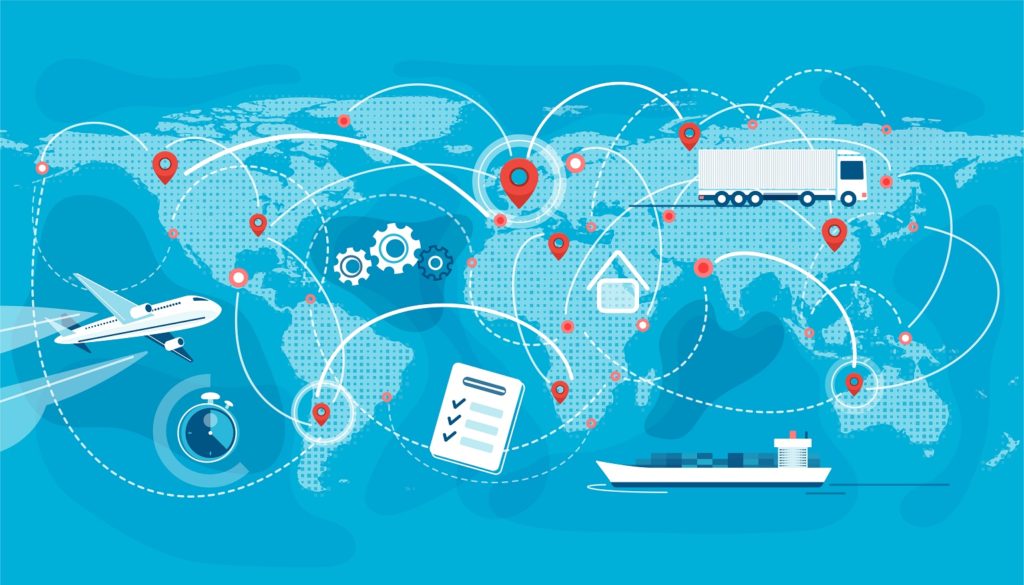
The supply chain for everything is tangle up to the extent it will take lots of time to function normally again.
Two articles describing the depth of issues:
- Analogy of turning off a complex computer system. Some of the hundreds of components won’t work when you throw the ‘on’ switch.
- Description of the demand side pressure on supply chain. All those trillions of federal dollars sloshing around have created demand which has overloaded distribution systems.
(Cross posted from my other blog, Nonprofit Update, because it will be helpful to understand broad supply chain issues for audits during the upcoming busy season.)
American Thinker – 12/11/21 – We broke everything in the name of Covid – Author ran a large IT department at one point in the past. Every few years they had to shut down the entire computer system so that the factory could go through maintenance of the electrical system.
There were hundreds of switches and routers and computers that had to be turned back on. Who knows how many hundreds of programs had to reboot.
There were always a number of things that did not start back up correctly. His rather subdued comment:
“Such systems don’t like having the power cycled off and on.”
The economy of the world is several orders of magnitude more complicated than the computer system for a large company.
He points out millions of companies with billions of employees all interacting with each other are necessary to keep the economy going.
We have seen a host of dimensions to the hubris displayed by political leaders, desk-bound regulators, alleged public health experts, and other supposed experts. One of the biggest aspects of the hubris on display is supposedly knowing who is “essential” and what people and jobs and companies are “non-essential.”
My expansion of his illustration:
- essential healthcare workers need masks,
- which are produced in a factory,
- which requires a lot of employees,
- who need lots of textiles and plastics,
- from other factories producing the textiles,
- who need cloth,
- which is raised by farmers,
- who need lots of supplies,
- which are imported from around the world.
Where does that leave us?
Let me again expand on the author’s discussion.
Break any one step in that entire supply chain and the frontline health care workers won’t have masks, or won’t have enough syringes, or won’t be able to work because their day care provider is closed, or won’t have a key medicine to make you better, or won’t be able to drive to work because their car is in the shop since the part that broke is not available anywhere in the entire country for the three weeks. Or two months.
Nobody anywhere in any business or company or service provider knows more than a narrow sliver of what goes into the supply chain that keeps them in operation. Nobody understands more than a minuscule part of their own industry, let alone other industries.
Politicians and bureaucrats have only the vaguest hint of anything.
In spite of their massive, staggering, astounding ignorance, our so-called leaders picked and chose what sectors of the economy to shut down. They turned off a random dozen switches in the computer room and expected the entire computer system to keep functioning.
Now we are well over a year into trying to turn on the overwhelmingly complex engine of the economy.
And the virus, for which we sacrificed the economy, is still here.
As is the damage caused by the politicians, bureaucrats, and public health officials.
Wall Street Journal – 12/17/21 – An Insider Explains the Supply-Chain Crisis – An executive who helps companies arrange shipping of containers has a number of observations on the tangled supply-chain.
His first-hand experience? It took five months to get a replacement stove when his stopped working.
One indication of the tangled mess is it used to take 71 days for a container to leave a port in China, transit to Los Angeles, get unloaded, transfer to Chicago, be emptied there, returned to Los Angeles, and return to the same port in China. That round-trip now takes 117 days or longer. Instead of 71 days it takes an additional 46, at least. That’s at least a 60% increase in round-trip transit time.
Oh, and the cost? A few years ago it was around $1,500 to get a container from China to California. Now it is $15,000. If you happen to be moving a container of laptops, phones, or highly machined parts, that cost can be absorbed. How about if you are a lower-cost retailer when the total value of a container is only running $15,000? Ouch.
Pandemic rules tangled up everything at one port in China, Yantian, which was shut down for several months in spring of 2021. That port handles one third more volume than the Port of Los Angeles. Take that out of production for a couple months and guess what? Everything is backed up.
The port systems are built to handle peak volume, which is from August through November, when everything is getting stocked for the holidays.
Demand for goods has increased. A couple months into the pandemic demand for durable goods (things like refrigerators, ovens, and stoves) increased, putting pressure on the supply chain. Several months after that demand for nondurables increased. Because of so much money sloshing around the economy and people were staying home so much, there was far higher demand for all goods beyond the normal peak season.
The entire supply chain has been running above peak capacity for a year and a half. No wonder everything is tangled up.
It will take a long time to untangle everything and get supply caught up with demand.